Embedded systems have revolutionized our interaction with technology by adding intelligence and connectivity to everyday devices. However, to enable these capabilities, custom digital logic circuits form the backbone. They provide essential functionalities such as processing and decision-making. While standard off-the-shelf components might suffice for some applications, there are numerous situations where they fall short in meeting specific requirements. Consequently, engineers often turn to designing custom logic circuits to meet these unique demands.
Creating custom logic circuits for embedded applications involves more than just basic knowledge of digital logic. It requires a comprehensive understanding of optimization techniques, design considerations, and practical implementation strategies. Therefore, this blog will delve into the various facets of designing custom logic circuits for embedded systems. We will cover their significance, key design principles, useful tools, and proven methodologies.
Fundamentals of Digital Logic
To create effective custom logic circuits, a solid understanding of digital logic fundamentals is essential. Digital logic circuits are built using logic gates. These gates perform basic operations based on input signals. Here’s a look at the key components:
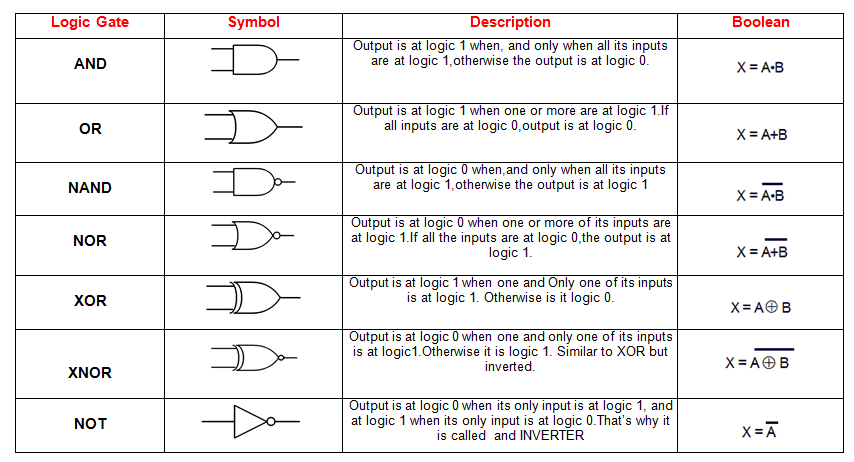
Logic Gates
Digital Logic gates are the basic building blocks of digital circuits. Each gate performs a specific logical operation based on its inputs. The fundamental logic gates include:
- AND Gate: Outputs true only if all inputs are true.
- OR Gate: Outputs true if at least one input is true.
- NOT Gate: Outputs the inverse of the input.
- NAND Gate: Outputs false only if all inputs are true (inverse of AND).
- NOR Gate: Outputs true only if all inputs are false (inverse of OR).
- XOR Gate: Outputs true if an odd number of inputs are true.
- XNOR Gate: Outputs true if an even number of inputs are true (inverse of XOR).
Combinational Logic
Combinational logic circuits produce outputs based solely on the current input values, with no memory of past inputs. Examples of combinational logic circuits include:
- Adders: Perform binary addition. Examples include half adders and full adders.
- Multiplexers (MUX): Select one input from multiple inputs based on control signals.
- Demultiplexers (DEMUX): Distribute a single input to multiple outputs based on control signals.
- Encoders: Convert multiple input signals into a smaller number of output signals.
- Decoders: Convert binary input signals into a larger number of output signals.
Sequential Logic
Sequential logic circuits have outputs that depend on both the current inputs and the previous states. They incorporate memory elements such as flip-flops and are used in applications that require data storage or state retention. Examples include:
- Counters: Track the number of events or pulses.
- Shift Registers: Store and shift data serially or in parallel.
- Finite State Machines (FSMs): Control the sequence of operations based on input signals and current state.
Why Use Custom Logic Circuits in Embedded Systems?
Custom logic circuits offer several advantages over standard, pre-designed components. These benefits make them particularly valuable in embedded applications where specific requirements must be met. Here are some of the key reasons to use custom logic circuits:
Optimized Performance
Custom logic circuits can be designed to meet the exact performance requirements of an application. By tailoring the circuit’s architecture, engineers can achieve the desired processing speed, response time, and power consumption, leading to an optimized solution.
Compact Size and Cost Efficiency
Custom circuits often result in smaller and more cost-effective designs by integrating only the necessary logic functions. This reduction in size and cost can be particularly advantageous in applications where space is limited or cost constraints are a significant consideration.
Enhanced Security
Embedded systems often require a high level of security, especially in applications involving sensitive data or critical operations. Custom logic circuits can implement unique, application-specific encryption or authentication algorithms, enhancing the overall security of the system.
Greater Flexibility
Using custom logic allows designers to create solutions that can be easily modified or expanded to accommodate changes in requirements or new functionalities. This flexibility is particularly useful in rapidly evolving fields such as IoT and consumer electronics.
Tailored Performance and Efficiency
One of the most significant advantages of custom logic circuits is their ability to deliver precisely the performance needed for a specific application. Standard components often come with additional features or capabilities that may not be required, consuming more power, taking up more space, and costing more than necessary. By designing custom logic circuits, engineers can include only the essential functions, reducing complexity and resource usage. This approach results in an optimized design that delivers the desired performance without any unnecessary overhead.
Reduced Power Consumption
Many embedded systems, such as wearable devices, sensors, and IoT gadgets, rely on battery power. In these cases, power consumption is critical, and every microampere counts. Custom logic circuits allow for fine-tuning power usage by minimizing switching activities, optimizing clock speeds, and using low-power components. By carefully selecting and designing each part of the circuit, engineers can significantly reduce power consumption, extending battery life and improving the overall efficiency of the device.
Smaller Footprint and Lower Costs
Space constraints are a common challenge in embedded applications, especially in compact devices like medical implants, smartwatches, and miniaturized sensors. Custom logic circuits enable engineers to integrate only the necessary logic functions, resulting in a smaller overall footprint. This reduction in size directly correlates with lower costs, as fewer materials and components are needed, and the simplified design may reduce manufacturing complexity. Moreover, custom circuits can be designed to use fewer pins and interconnections, further contributing to cost savings.
Steps in Designing Custom Logic Circuits
Creating a custom logic circuit involves several key steps, from defining the requirements to validating the final design. Understanding each step in the design process is essential for ensuring a successful outcome.
Define the Requirements
The first step in designing a custom logic circuit is to define the specific requirements of the application. This includes understanding the desired functionality, performance constraints, power requirements, and cost considerations. Gathering this information will guide the design process and help identify the most suitable logic elements.
Develop a Logic Diagram
After defining the requirements, the next step involves creating a logic diagram that outlines the circuit’s basic structure. This diagram should incorporate all the necessary logic gates and components, along with their connections. By serving as a blueprint for the design, the logic diagram not only visualizes the circuit but also helps in identifying potential challenges early in the process. Thus, it lays the foundation for a more effective and streamlined design phase.
Choose the Design Methodology
There are several methodologies for designing custom logic circuits, including:
- Gate-Level Design: Involves using basic logic gates to build the circuit from the ground up. This approach provides a high level of control and optimization but can be time-consuming for complex designs.
- Hardware Description Languages (HDLs): Such as VHDL or Verilog, HDLs allow designers to describe the behavior and structure of the circuit at a higher level of abstraction. HDLs are well-suited for complex designs and can be used with automated tools for synthesis and simulation.
- Schematic Capture: Involves creating a visual representation of the circuit using specialized software tools. Schematic capture is particularly useful for smaller designs or when working with existing components.
Simulate the Design
Once the initial design is complete, simulate the circuit to verify its functionality and performance. Simulation tools, such as ModelSim or Xilinx Vivado, can help identify errors or inefficiencies in the design, allowing engineers to make necessary adjustments before moving on to the implementation stage.
Optimize the Circuit
Based on the simulation results, optimize the circuit to meet the desired performance, power, and cost constraints. This may involve adjusting the logic gate arrangement, modifying the circuit architecture, or selecting different components.
Implement the Design
After optimization, implement the design using the chosen methodology. For gate-level designs, this may involve creating the circuit using discrete components or an FPGA. For HDL-based designs, synthesis tools can generate the final implementation for an FPGA or ASIC.
Test and Validate
The final step is to test and validate the custom logic circuit to ensure it meets the specified requirements. This involves verifying the circuit’s functionality, performance, and reliability under different operating conditions.
Design Considerations for Custom Logic Circuits in Embedded Systems
When designing custom logic circuits for embedded applications, several key considerations must be considered to ensure success. These considerations include:
Power Consumption
Power consumption is often a critical concern in embedded systems, particularly for battery-operated devices. Designing low-power logic circuits involves minimizing switching activity, optimizing the use of low-power components, and using power-saving techniques such as clock gating.
Timing and Latency
In real-time embedded applications, timing is crucial. Ensuring that the logic circuit meets the required timing constraints involves careful consideration of propagation delays, setup and hold times, and clock skew. Tools such as timing analysis software can help identify potential timing issues early in the design process.
Area and Cost
Minimizing the size and cost of the custom logic circuit is essential for many embedded applications, especially in consumer electronics. Designers can reduce the circuit area by using efficient logic gate arrangements, selecting compact components, and integrating multiple functions into a single circuit.
Scalability and Flexibility
Custom logic circuits should be designed with scalability and flexibility in mind to accommodate future changes or additions to the system. This involves modular design techniques, reusable components, and considering potential future requirements during the initial design phase.
Environmental Conditions
Embedded systems often operate in challenging environments, such as extreme temperatures, humidity, or vibration. The design of custom logic circuits must consider these environmental conditions to ensure reliable operation. This may involve selecting robust components, using protective coatings, or implementing error detection and correction mechanisms.
Tools for Designing Custom Logic Circuits
Several tools are available to assist in designing custom logic circuits for embedded applications. These tools include:
- HDL Simulators
HDL simulators like ModelSim and Synopsys VCS allow designers to simulate the behavior of their custom logic circuits and verify their functionality. These tools provide a high level of control and flexibility, making them ideal for complex designs. - FPGA Development Boards
FPGA development boards, such as those from Xilinx or Altera, provide a platform for implementing and testing custom logic circuits in hardware. These boards offer a range of features, including configurable logic blocks, high-speed I/O, and memory interfaces, making them suitable for prototyping and development. - Schematic Capture Tools
Schematic capture tools like KiCad and OrCAD enable designers to create visual representations of their custom logic circuits. These tools provide a user-friendly interface for designing, simulating, and documenting the circuit, making them particularly useful for smaller designs. - Logic Analyzers
Logic analyzers are used to test and debug custom logic circuits by capturing and analyzing digital signals. These tools provide valuable insights into the circuit’s behavior and performance, helping engineers identify and resolve issues.
Examples of Custom Logic Circuits in Embedded Applications
Custom logic circuits are used in a wide range of embedded applications, including:
- Motor Control
In motor control applications, custom logic circuits can be used to implement precise control algorithms, such as PID control, pulse-width modulation (PWM), and feedback loops. These circuits help improve motor efficiency, reduce power consumption, and enhance performance. - Sensor Data Processing
Custom logic circuits can be designed to process sensor data in real-time, filtering noise, and extracting useful information. For example, a custom circuit could implement a digital filter to remove unwanted noise from a sensor signal, improving the accuracy of the data. - Communication Protocols
Many embedded systems require custom logic circuits to implement communication protocols, such as UART, SPI, I2C, or custom protocols for specific applications. These circuits enable reliable and efficient communication between different components or devices.
Key Steps in Designing Custom Logic Circuits
Creating a custom logic circuit requires following a structured design process, which involves several essential steps. These steps include defining requirements, developing a logic diagram, choosing a design methodology, simulating the circuit, optimizing the design, implementing the solution, and testing it thoroughly. Let’s explore each step in detail.
Define Requirements
To begin with, defining the requirements serves as the most crucial initial step in designing a custom logic circuit. Engineers need to clearly understand the application’s specific needs, including desired functionality, performance objectives, power constraints, cost limitations, and environmental considerations. By gathering this detailed information early, they can guide the entire design process, making informed decisions regarding the circuit’s architecture, components, and technologies.
Develop a Logic Diagram
After defining the requirements, the next step is to develop a logic diagram that outlines the circuit’s basic structure. This diagram acts as a blueprint, representing all the logic gates, components, and connections necessary to achieve the intended functionality. Therefore, creating a logic diagram helps engineers visualize the design while identifying potential challenges or bottlenecks early in the process.
Choose the Right Design Methodology
There are several methodologies for designing custom logic circuits, each with advantages and drawbacks:
- Gate-Level Design: Involves manually constructing the circuit using basic logic gates like AND, OR, and NOT. This approach offers maximum control and optimization but can be time-consuming for complex designs.
- Hardware Description Languages (HDLs): HDLs such as VHDL and Verilog allow engineers to describe the circuit’s behavior and structure at a higher level of abstraction. HDLs are suitable for complex designs and can be used with automated tools for synthesis and simulation.
- Schematic Capture: Schematic capture tools provide a visual representation of the circuit, making it easier to understand and modify. These tools are especially useful for smaller designs or when working with existing components.
Simulate the Circuit
Before moving to implementation, simulating the circuit to verify its functionality and performance is crucial. Simulation tools like ModelSim, Xilinx Vivado, and Synopsys VCS allow engineers to test their designs in a virtual environment, identifying errors, bottlenecks, or inefficiencies that need to be addressed. Simulation ensures that the circuit behaves as expected and meets all the requirements before committing to hardware.
Optimize the Design
Based on the simulation results, engineers can proceed to optimize the circuit to meet performance, power, and cost constraints. For instance, they might rearrange logic gates, choose different components, or adjust the circuit’s architecture. By carefully fine-tuning the design, engineers can achieve the ideal balance between performance, power consumption, size, and cost.
Implement the Circuit
Once the optimization is complete, the next step is to implement the circuit using the chosen methodology. Engineers might create gate-level designs using discrete components or employ an FPGA (Field-Programmable Gate Array) for the implementation. For designs based on Hardware Description Languages (HDL), engineers utilize automated tools to synthesize the final implementation for an FPGA or ASIC (Application-Specific Integrated Circuit).
Test and Validate
Following implementation, testing and validating the custom logic circuit become crucial steps. Engineers must ensure the circuit meets all specified requirements by verifying its functionality, performance, and reliability under various operating conditions. To achieve this, they often use tools such as logic analyzers, oscilloscopes, and other testing equipment to analyze the circuit’s behavior and address any issues that arise.
Tools and Methodologies for Designing Custom Logic Circuits
Designing custom logic circuits requires a variety of tools and methodologies, each suited to different aspects of the design process. Some of the most commonly used tools include:
Hardware Description Languages (HDLs)
HDLs like VHDL (VHSIC Hardware Description Language) and Verilog are widely used for designing custom logic circuits. These languages allow engineers to describe the circuit’s behavior and structure in a high-level, textual format. HDLs are particularly useful for complex designs, enabling the use of automated synthesis and simulation tools.
Schematic Capture Tools
Schematic capture tools like KiCad, OrCAD, and Eagle provide a visual interface for creating circuit diagrams. These tools allow engineers to design, simulate, and document their circuits, making them particularly useful for smaller designs or when working with existing components.
FPGA Development Boards
FPGA development boards, such as those from Xilinx, Altera, or Lattice, provide a platform for implementing and testing custom logic circuits in hardware. These boards offer various features, including configurable logic blocks, high-speed I/O, and memory interfaces, making them suitable for prototyping and development.
Simulation Tools
Simulation tools like ModelSim, Xilinx Vivado, and Synopsys VCS allow engineers to test their custom logic circuits in a virtual environment. These tools provide valuable insights into the circuit’s behavior, performance, and timing, helping engineers identify and resolve issues before moving to hardware.
Logic Analyzers
Logic analyzers play a crucial role by capturing and analyzing digital signals, thereby providing real-time data on a circuit’s operation. Consequently, these tools prove invaluable for debugging and testing custom logic circuits. By enabling engineers to monitor and verify the behavior of each logic gate, signal path, and component, logic analyzers facilitate a deeper understanding of the circuit’s functionality and assist in pinpointing any issues that arise.
Challenges in Designing Custom Logic Circuits
While designing custom logic circuits offers numerous benefits, it also presents several challenges that engineers must overcome:
Complexity Management
Designing custom logic circuits can be complex, especially for large-scale designs with multiple interconnected components. Engineers must manage this complexity by using modular design techniques, maintaining clear documentation, and employing rigorous testing and validation methods.
Power and Thermal Management
Power consumption and thermal management remain critical concerns in embedded systems. To minimize power usage and effectively dissipate heat, engineers must design custom logic circuits that prevent overheating and ensure reliable operation. Therefore, they often use low-power components, optimize clock speeds, and implement power-saving techniques.
Timing and Synchronization
Moreover, timing and synchronization play a vital role, especially in real-time embedded applications. Engineers must manage propagation delays, setup and hold times, and clock skew carefully to ensure proper circuit operation. To address these challenges early in the design process, they rely on timing analysis tools to identify potential issues and make necessary adjustments.
Cost and Resource Constraints
Custom logic circuits must be designed to meet cost and resource constraints, especially in consumer electronics and other price-sensitive markets. Engineers must balance performance, power, size, and cost requirements to create a competitive and viable solution.
Debugging and Validation
Debugging and validating custom logic circuits can be challenging, particularly when dealing with complex designs or real-time constraints. Engineers must use various tools and techniques, such as simulation, logic analyzers, and in-circuit debugging, to identify and resolve issues.
Best Practices for Creating Custom Logic Circuits
To ensure a successful custom logic circuit design, engineers should follow these best practices:
Start with a Clear Specification
Before beginning the design process, engineers should develop a detailed specification that outlines all the requirements, constraints, and performance objectives. This document will guide the entire design process and help ensure the final circuit meets all the necessary criteria.
Use Modular Design Techniques
Using modular design techniques significantly helps manage complexity by breaking the circuit into smaller, self-contained blocks. Each block can then be developed, tested, and optimized independently, which simplifies debugging and validation. Moreover, this approach facilitates easier future modifications or upgrades, ensuring long-term adaptability of the design.
Optimize for Power and Performance
To achieve the desired performance, engineers should prioritize optimizing for power and performance. Selecting the right components, minimizing switching activities, and employing efficient clock management techniques are all crucial strategies. These efforts not only help extend battery life but also reduce heat generation and ensure the circuit meets all performance requirements..
Conduct Thorough Testing and Validation
Subsequently, conducting thorough testing and validation becomes critical to the success of any custom logic circuit. Utilizing various tools such as simulation software, logic analyzers, and in-circuit debugging helps verify the circuit’s functionality, performance, and reliability under different operating conditions. This step ensures the circuit operates as intended in all scenarios.
Document the Design Process
Finally, documenting the design process is essential for maintaining and updating custom logic circuits. It is important for engineers to record all design decisions, specifications, and testing results to create a comprehensive reference. This documentation proves invaluable for future development, upgrades, or troubleshooting, allowing for a smoother workflow and easier management of the circuit over time.
Conclusion
Creating custom logic circuits for embedded applications is a powerful way to optimize performance, reduce power consumption, and meet specific design requirements. By understanding the basics of digital logic, following a structured design process, and considering key factors such as power consumption, timing, and cost, engineers can develop effective and reliable custom logic circuits tailored to their unique needs. Whether designing a motor control system, processing sensor data, or implementing a communication protocol, custom logic circuits offer the flexibility and optimization needed to achieve success in embedded systems.
To have a better understanding of IoT Protocols, we recommend using Smowcode to boost your productivity and create great products 10x faster.
Try Smowcode for free and Boost your Productivity by 10x. : https://smowcode.com/
Do go through our other blogs to understand IoT concepts: https://blog.smowcode.com/smart-connectivity-wi-fi-in-the-iot-era/
Link to Modbus Blog: https://blog.smowcode.com/understanding-modbus-in-industrial-iot/